
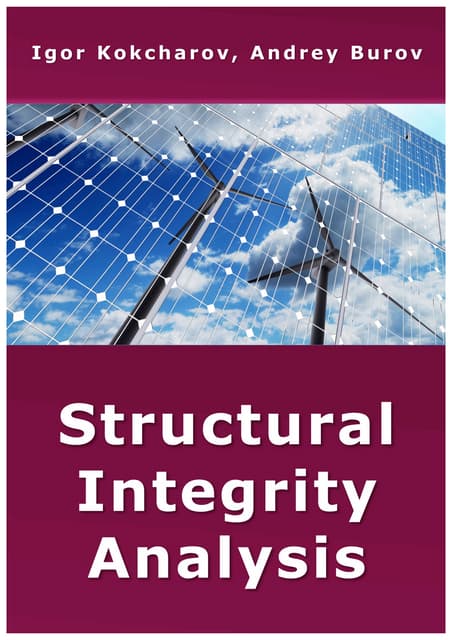
#Structural integrity crack#
In this approach, material resistance is expressed in terms of tensile properties (yield and tensile strengths) and fracture toughness (resistance of a material against any crack growth). In fracture mechanics-based approach, unlike yield point-based design approaches, a material should withstand the maximum applied load when of a crack-like flaw exists. Optimum selection and use of structural materials in order to reduce the weight, manufacturing and running costs of almost all engineering structures, requires profound understanding of failure mechanisms. However, such yield-point-based designs, which incorporate high safety factors, are not an optimum approach for all engineering structures. The Eiffel Tower is more that 115 years old and was designed and built long before the engineers started developing the basic concepts of fracture mechanics. This was the beginning of a new field in engineering called Fracture Mechanics. Substantial amount of experimental and theoretical work on failure mechanisms was undertaken in mid 19th century. Hence, researchers tried to understand the mechanisms of such brittle fractures, which apparently occurred due to the presence of crack-like flaws in the weldment and bulk steels. These catastrophic failures were attributed to the presence of crack-like flaws in the welded joints, the use of steels with a low resistance to crack propagation (particularly in cold sea water) and poor joint design. However, the catastrophic failure of some the naval ship and tankers in cold seawater during World War II, led to a broad research program in order to find out the cause of such failures. Until early 19th century, the design engineers relied on using large safety factors in order to overcome the uncertainty associated with the actual strength of various components and their joints due to inevitable and undetectable internal defects. bridges, Ferris Wheels or a car chassis, may contain flaws and defects, which can compromise the strength of the structure drastically.
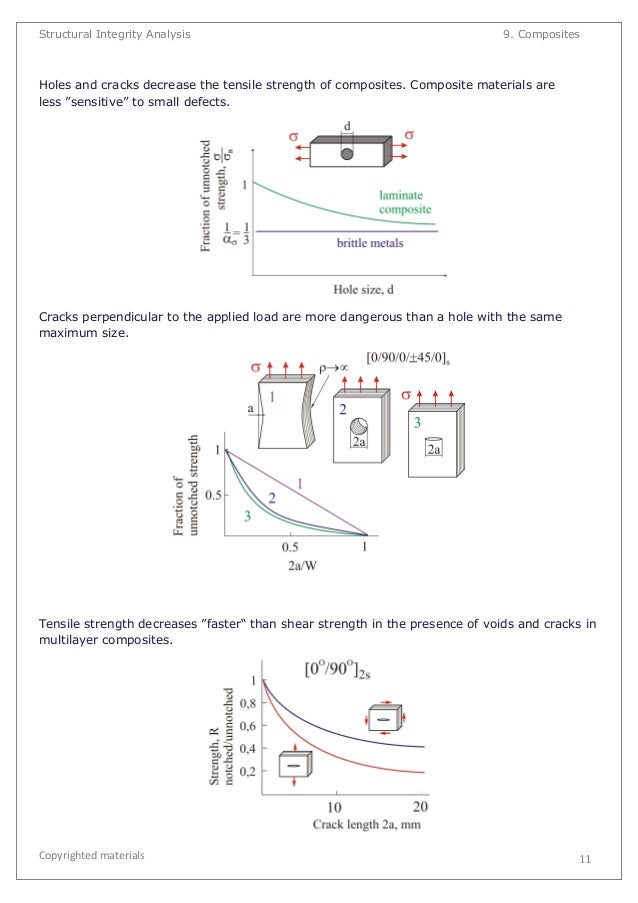
The components and welded joints in engineering structures, e.g.
#Structural integrity free#
This approach is based on the assumptions that (1) the component is free from any flaws and defects and (2) the safety factor would compensate for any unexpected overloading or deterioration of the component during its service life. The ratio of the yield strength to the applied stress is often called safety factor, typically in order of 1.5 to 3. In the conventional design approach, maximum applied stress should not exceed a certain fraction of the yield strength (i.e. If the former appears to be greater than the latter, then the component is considered to be fit for service, otherwise, modification in design or the use of another material with a higher strength is required. Structural Integrity Assessment is an approach to assess whether a structure is fit to withstand the service conditions safely and reliability throughout its predicted lifetime.Įstablished philosophy behind the design of any structural component is to ensure that the strength of the material, of which the component is made of, is higher than the maximum applied stress in service. Integrity is a term which refers to the quality of being whole and complete, or the state of being unimpaired.
#Structural integrity full#
Our simulation solutions help you predict loads on full product level that can be cascaded down to the subsystem and component levels to assess critical stresses and lifetime behavior.Structural Integrity Assessment of Engineering Components Afshin Motarjemi and Amir Shirzadi Background Our testing solutions help you obtain high-quality data quickly with confidence and in an automated way, as well as set realistic and accurate design targets for damage usage scenarios. Our test and simulation solutions deliver an industry-proven durability engineering process.

To deal with increasingly complex equipment, that can also be delivered in a wide array of differing configurations, durability engineers need an effective process that includes full load histories, as well as accurate models and fatigue life prediction methodologies. Most machines operate at peak capacity around the clock, making structural integrity and durability critical functional performance aspects during machine development. As a result, new production machines need to be engineered to handle increasing loads that result from added torque and power, while continuing to avoid downtime and malfunctions. Manufacturers are constantly looking to increase out and improve productivity.
